Un pozo somero que iba a ser perforado en forma direccional fue planeado utilizando información de un pozo de límite.
Esta información sugería fuertemente que se encontrarían una zona con pérdida de circulación, unos pocos metros debajo de donde el casing sería colocado. Este pozo debía ser perforado en el mismo pad que otro pozo que tuvo una surgencia en la década del 50 durante operaciones de perforación; la zona de blowout se encontraba próxima a la zona proyectada de pérdida de circulación para el nuevo pozo.
Se consideró perforar a través de esta zona y realizar una entubación intermedia. Luego de que la columna fuera colocada a través de la zona de pérdida de circulación, la perforación podría comenzar sin mayores preocupaciones. Sin embargo, esto reduciría considerablemente el diámetro de producción de la tubería. La operadora decidió perforar a través de la zona de pérdida de circulación y controlar el peso del lodo asegurándose de que el pozo se mantuviera lleno.
El uso de un perforador automático era necesario para monitorear la velocidad de penetración, la carga en el gancho, la presión de la columna ascendente, las emboladas de la bomba, la velocidad del rotary, el peso y torque en el trépano. Factores limitativos usados por el perforador automático fueron utilizados para alcanzar la velocidad de penetración óptima.
La presión del lodo fue medida con un dispositivo de señalización ubicado dentro del standpipe del equipo y de allí enviado al perforador automático. La carga en el gancho fue medida por otro dispositivo de señalización anexado al anclaje. De la misma forma, dispositivos para torque y RPM se anexaron a la mesa rotativa del equipo. Uno o dos de estos parámetros controlaban el cuadro de maniobras de ROR por el perforador automático y el progreso de la sarta de perforación en el fondo del pozo.
Antes de que el conjunto de fondo, el motor para circular el lodo y el trépano estuvieran en el fondo, el contratista de perforación accionó la bomba de lodo. El peso en el trépano es difícil de medir en las operaciones de perforación direccional. Mientras se perfora en forma no vertical con un motor para circular el lodo, la medición de su presión se vuelve crítica con respecto al alcance del óptimo rendimiento del torque y las revoluciones por minuto.
El hoyo de superficie fue perforado verticalmente; un casing de superficie de 9 5/8 in. 36 lbs/pie K55 fue colocado y cementado a una profundidad de 209 pies. Esto fue testeado sin dificultad. Luego, el conjunto de fondo se adaptó a una tasa de aumento del ángulo de 3º/100 pies y se utilizó una barra de sondeo de 3 ½ in. El trépano era de 8 ½ in.y el BHA utilizaba un motor para circular el lodo y una válvula de contrapresión. El diámetro exterior del conjunto de fondo era de 6 ½ in, y su longitud total era de aproximadamente 119 pies.
El equipo de perforación utilizaba un vástago y el hoyo de 8 ½ in fue perforado verticalmente a una profundidad de 384 pies. Se creía que la zona de pérdida de circulación se encontraba entre los 500 y los 750 pies de profundidad vertical total.El peso del lodo era cuidadosamente vigilado. No se generaron problemas mientras la perforación progresaba a través de la zona de pérdida de circulación.
Basándose en la información de la década del 50 se optó por un peso de lodo de 11.1 lbs/galón, debido al blowout ya mencionado.Luego de perforar por la zona de pérdida de presión sin problemas de well control, el peso del lodo se redujo para adaptarse a la zona productiva de baja presión, en el fondo del pozo. Mientras avanzaba la perforación, el pozo fue circulado normalmente.
Luego de que el foso fue perforado direccionalmente a una profundidad medida de 1017 pies, su ángulo fue de aproximadamente 22º. La proporción de cambio en el ángulo del hueco del pozo fue de 384 pies profundidad vertical a 22º a 1017 pies de profundidad medida, cerca de 3/100º
Click en la imagen
Luego se decidió realizar una maniobra de limpieza.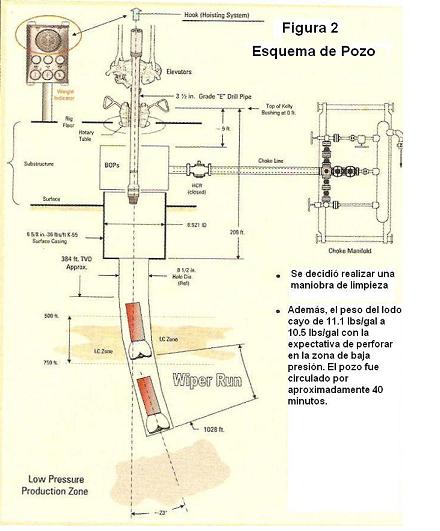
Previo a esto, el peso sobre el trépano era de 12,000 libras.
El trépano llegó a 0 lbs mientras circulaba, tomando para esto 3 minutos. Con 0 libras de peso sobre el trépano, la bomba funcionando y el BPV abierto, se registró una carga en el gancho de 30000 libras.
Click en la imagen
Cuando la bomba fue apagada, el BPV se cerró. El conjunto de fondo y la columna perforadora flotaron con presión hidrostática y la carga en el gancho debía reducirse en 6000 libras. Luego de que el vástago fuera retirado, la sarta de perforación fue sacada. La carga en el gancho reportada por el perforador automático fue de 28000 libras. Es importante destacar que mientras el Perforador automático no estaba siendo utilizado para controlar la velocidad de penetración, continuaba recibiendo y almacenando señales. 8 tiros fueron sacados en 20 minutos. Los registros de carga en el gancho se mantuvieron considerables pero no fueron notados por el perforador ni por el company man.
Las bombas continuaron funcionando durante la maniobra de retirada de los tiros 1 al 5, llenado el pozo continuamente. Luego de que el Tiro 5 fue retirado, las bombas fueron apagadas y permanecieron así mientras los dos tiros siguientes eran sacados. No se utilizó ni un tanque de maniobra ni un indicador del nivel de lodo.El octavo tiro fue sacado y permaneció suspendido en el montacargas. Las bombas se encendieron durante dos minutos aproximadamente, luego se apagaron. La terminó con el trépano en las proximidades de la zona de Perdida de circulación.
En los 15 minutos siguientes 8 tiros volvieron al pozo, aproximadamente 1 tiro cada 2 minutos. El vástago fue reemplazado y la operación de perforación continuó.Mientras estas tareas continuaban, una serie de hechos fueron desatendidos. Durante la maniobra de retirada se registraron significativas cargas en el gancho.Con el trépano otra vez en el fondo el peso del lodo bajó de 11.1 lbs/gal a 10.5 lbs/gal con las expectativas de perforar en la zona de baja presión. El hueco del pozo fue circulado aproximadamente por 40 minutos.
El pozo fue perforado direccionalmente de 1017 pies MD a 1285 pies MD en 7 horas; un promedio de 38 pies/hora. El ángulo fue de 30º y su profundidad total verdadera fue de 1113 pies. Luego las tareas de retirada comenzaron para facilitar el perfilaje. El pozo fue circulado. El vástago fue izado y bajado intermitentemente mientras que rotaba la columna de perforación.
Click en la imagen
La bomba fue apagada y 4 de los tiros fueron rápidamente sacados:
Tiro 1: Carga de gancho según perforador automático: 37000 lbs
Carga de gancho calculado: 16700 lbs.
Tiro 2: Carga de gancho según perforador automático: 39000 lbs
Carga de gancho calculado: 16200 lbs
Tiro 3: Carga de gancho según perforador automático: 38000 lbs
Carga de gancho calculado: 15700 lbs
Tiro 4: Carga de gancho según perforador automático: 36000 lbs
Carga de gancho calculado: 15200 lbs
Luego de la primera hora los tiros fueron retirados la bomba fue encendida nuevamente.
Luego de sacar el 5º tiro la bomba fue apagada, antes de que el 6º tiro fuera izado.
Tiro 5: Carga de gancho según perforador automático: 32000 lbs
Carga de gancho calculado: 14700 lbs
Tiro 6: Carga de gancho según perforador automático: 34000 lbs
Carga de gancho calculado: 14200 lbs
El tiro 7 y el 8 fueron sacados rápidamente, la carga en el gancho era alta, más de lo que debía ser.
Tiro 7: Carga de gancho según perforador automático: 29000 lbs
Carga de gancho calculado: 13900 lbs
Tiro 8: Carga de gancho según perforador automático: 28000 lbs
Carga de gancho calculado: 13100 lbs
Durante la maniobra de retirada del 9º tiro, la bomba fue encendida durante dos minutos y luego apagada.
Tiro 9: Carga de gancho según perforador automático: 28000 lbs
Carga de gancho calculado: 12600 lbs
Del tiro 10 al 13 fueron sacados en 25 minutos.
Tiro 10: Carga de gancho según perforador automático: 28000 lbs
Carga de gancho calculado: 12100 lbs
Tiro 11: Carga de gancho según perforador automático: 28000 lbs
Carga de gancho calculado: 11600 lbs
Tiro 12: Carga de gancho según perforador automático: 28000 lbs
Carga de gancho calculado: 11100 lbs
Mientras el tiro 13 estaba siendo extraído, la carga en el gancho según el perforador automático, cayó 7000 libras mientras la calculada era de 10500.
El pozo comenzó a fluir a través del espacio anular. En lugar de armar la BOP, el perforador intentó volver a colocar el vástago, pero no lo logro. Entonces, la descarga de gas proveniente del pozo se encendió. Mientras las llamas crecían, el enganchador corría serios riesgos. Su único medio de escape era por la Línea de escape, pero finalmente el fuego consumió el cable. Más tarde se confirmó que la BOP nunca había sido cerrada.
Claramente, los problemas del well control se habían producido por la rápida extracción de la tubería de perforación durante la maniobra de limpieza. La carga en el gancho durante la perforación y circulación registradas y controladas, por lo general coincidían.
A medida que las operaciones de retirada estaban en marcha había significativas discrepancias entre los registros calculados por el Perforador automático y los cálculos de la carga del gancho.
Además, los esfuerzos del contratista de perforación para monitorear los volúmenes de fluidos mientras se extraía la tubería de perforación fueron nulos. Las bombas de lodo solo fueron prendidas hasta que el lodo se derramaba fuera del pozo y luego, apagadas.Durante la maniobra de sacado, el pozo fue pistoneado. A medida que el conjunto de fondo se aproximaba a la zona con Pérdida de Circulación, las cargas no estaban como debían.
La política del contratista requería que velocidades de izaje se hicieran a velocidades controladas para no inducir una entrada de fluidos de perforación. Si hubo alguna indicación de pistoneo o de entrada de fluidos de la formación, las medidas para controlar el pozo deberían haberse tomado inmediatamente.
Además, el lodo debía ser circulado y acondicionado en o cerca del fondo del pozo salvo que las condiciones impidieran el descenso del conjunto de pozo al fondo.
Previo a este incidente, existían ciertas preocupaciones sobre la integridad del zapato de casing de superficie 9 5/8 36 lbs/pie K55. En una situación de Well Control, un cierre fuerte podría haber comprometido su integridad. El perforador automático brindó información crucial al contratista y al company man pero fue desatendida por ambos. Este último tenía la información disponible para el. El contratista debería haber sabido monitorear los volúmenes de lodo y mantener el hueco del pozo adecuadamente lleno durante la operación de retirada y tripping. Un equipo competente debería haber sabido como estaban las cargas.
Solo los datos del perforador automático deberían haber alcanzado para alertarlos. Lo correcto habría sido cerrar el pozo y tratarlo competentemente. Evidentemente, cualquier enganchador se habría encontrado en peligro de ser alcanzado por el fuego. No tendría ningún medio confiable de escape mientras se desarrollaba este evento. Además, las líneas de comunicación entre el company man y el contratista probaron ser extremadamente ineficaces.
La información crítica del perforador automático fue completamente ignorada, incluyendo a un contratista implementando sus propias políticas de well control. La comunicación y los malentendidos entre el operador y el contratista, los esfuerzos para trabajar rápidamente, el uso de equipos de seguridad inapropiados y supervisión y conducción inadecuadas de los empleados son, por lo general, las razones más habituales.
Traducido por staff de PetrolNews.
Fuente: Drilling Contractor
6121 lecturas | Ver más notas de la sección Novedad Técnica