Alexander Sas-Jaworsky II, SAS Industries Inc., Houston. Este capítulo ofrece un panorama de los desarrollos comerciales de la tubería flexible, incluyendo la fabricación de productos tubulares flexibles de fresado continuo. Asimismo, veremos la reacción de la tubería ante las diversas tensiones y fuerzas a las que son sometidas durante operaciones normales de reacondicionamiento de pozo.
En capítulos anteriores se han tratado los desarrollos de los equipos y los lineamientos básicos de seguridad que deben contemplarse durante los servicios con tubería flexible (CT, por sus siglas en inglés). Aunque las modificaciones realizadas en los equipos han mejorado la confiabilidad de su desempeño y servicio, los últimos avances en tecnología son el resultado de mejoras en su fabricación y manejo.
La tecnología moderna de tubería flexible puede remontarse a la labor emprendida por los equipos de ingeniería de las Fuerzas Aliadas durante la Segunda Guerra Mundial. El proyecto PLUTO (cuyas siglas en inglés significan Ductos por Debajo del Océano) era un plan secreto de invasión de las Fuerzas Aliadas que consistía en el montaje de ductos a través del Canal de la Mancha, desde Inglaterra hasta Francia. Al concluir el Proyecto PLUTO, las Fuerzas Aliadas instalaron 17 ductos para suministrar combustible a las fuerzas Aliadas de invasión. La mayoría de ductos se construyó con tubos de plomo de 3" de diámetro interno (ID, por sus siglas en inglés) y un espesor de pared (WT, por sus siglas en inglés) de 0,175" reforzado con una cobertura exterior de cable trenzado para mayor contención.
Los 11 ductos compuestos por tubos de plomo fueron enrollados alcanzando una extensión total de alrededor de 48 kilómetros (30 millas). Los seis restantes se fabricaron soldando tubos de acero de 3" de diámetro interno, 0,212" de espesor de pared y 12,2 metros (40 pies) de largo para formar tuberías de 1.219 metros (4.000 pies). Estos tramos de 1.219 metros se soldaron entre sí por los extremos y se enrollaron en carretes de extensiones continuas de entre 48 y 113 kilómetros (30 y 70 millas) para su transporte. Todos los ductos PLUTO se enrollaron en tambores flotantes de aproximadamente 12 metros (40 pies) de diámetro con alrededor de 18 metros (60 pies) entre los rebordes. El éxito del enrollado y de la instalación de los ductos a mediados de la década de 1940 preparó el camino para la tecnología actual de tubería flexible.
Desarrollo de la Tubería Flexible Pero lamentablemente, este concepto de perforación con tubería flexible tenía una profundidad límite de 914 metros (3.000 pies) y sin el respaldo de la industria petrolera canadiense, esta área de desarrollo de CT llegó a su fin en 1978.
La llegada de los servicios petroleros con tubería flexible a comienzos de la década de 1960 requirió el desarrollo de tubos de menor diámetro externo que pudieran resistir las tensiones y la deformación al enrollarlos en un carrete de diámetro reducido. Los pioneros en el desarrollo y fabricación de tubería flexible intentaron aplicar técnicas de fabricación similares a las empleadas en el Proyecto PLUTO. En 1962, se fabricó el primer carrete de gran escala para tubería flexible utilizando un acero con niobio muy dúctil y de baja aleación. La empresa Great Lakes Steel Co. de Michigan, Detroit, laminaba la placa de acero a un espesor de 0,125" y la compañía Standard Tube Co., también de Detroit, la fresaba en tuberías de 1,315" de diámetro externo.
Los tubos fresados eran de solamente 15 metros (50 pies) y debían soldarse entre sí mediante un proceso combinado de Gas Inerte y Electrodo de Tungsteno (TIG, por sus siglas en inglés) y Gas Inerte y Aporte de Metal (MIG, por sus siglas en inglés). Posteriormente, el tubo se enrollaba en un carrete de 2,7 metros (9 pies) de diámetro. Los resultados de esta primera generación de tubería flexible no demostraron de manera acabada todo el potencial de esta tecnología. No obstante, dejó entrever cuán beneficiosa sería en los servicios de pozo de petróleo y gas.
La compañía Republic Steel, de Brooklyn, Nueva York fabricó la primera tubería en extensiones continuas utilizando un acero de alta ductilidad. El acero era un material de Alta Resistencia y Baja Aleación (HSLA, por sus siglas en inglés) y, salvo modificaciones menores, sentó las bases para la fabricación de la tubería flexible de hoy en día. El acero que tenía un límite elástico que oscilaba entre los 40.000-psi (40-ksi) y los 50.000-psi (50-ksi) venía en placas de 0,049" de espesor. La tubería se fresaba en tramos que variaban entre los 85 y los 610 metros (250 y 2.000 pies) y las sartas se ensamblaban soldando sus extremos mediante las técnicas TIG y MIG. Luego la tubería continua se enrollaba en carretes de 48" de diámetro.
Aunque en un principio el sistema de tubería flexible de Brown Oil Tool creado en 1964, fue construido para tuberías de ¾" de diámetro externo, en los tres años siguientes el sistema se modificó para correr tuberías de ½" de diámetro externo. En 1967, Bowen Tools produjo la segunda generación del sistema de tubería flexible diseñado en un principio para correr tuberías de ½" y ¾" de diámetro externo. A comienzos de la década de 1970, este sistema también sufrió modificaciones para el manejo de tuberías de 1" de diámetro externo.
Southwestern Pipe Inc. Comenzó la fabricación de tubería de extensión continua para CT en 1969. Aunque la resistencia del acero variaba todavía entre los 50-ksi y 55-ksi, las mejoras alcanzadas en su fabricación y tratamiento aumentaron significativamente el desempeño general del tubo. En esa época, Southwestern Pipe se convirtió en el proveedor líder de CT para la industria de reacondicionamiento concéntrico de pozo.
Durante comienzos de la década de 1970, se amplió la gama de servicios prestados con tubería flexible de 1" de diámetro externo, yendo desde el lavado de arena y la descarga de pozos someros a servicios más exigentes a mayor profundidad. Desafortunadamente, la resistencia del material y las numerosas soldaduras necesarias para la tubería continua de 1" de diámetro externo no pudieron resistir los repetidos ciclos de flexión y las altas cargas de tracción asociados a carreras de CT a mayor profundidad. Durante la década de 1970, la reputación de la tubería flexible en la industria del petróleo y el gas se resintió. La falta de confianza de los usuarios fue cada vez mayor debido a las fallas de las soldaduras, los desperfectos en los equipos y las situaciones de pesca de tubería flexible en los pozos.
Como la industria estadounidense de CT lograba progresar en los servicios de reacondicionamiento concéntrico de pozo, una empresa canadiense llamada FlexTube Service Ltd. promovió el concepto de perforación con tubería flexible. En 1976, comenzaron a perforar pozos de 366 a 518 metros (1.200 a 1.700 pies) de profundidad con diámetros internos de 6 ½" utilizando tubos flexibles de 2 3/8" de diámetro externo, para compañías operadoras en Alberta, Canadá. La columna de perforación de 2 3/8" de diámetro externo se construyó soldando los extremos de tubos X-42 de 12,19 metros (40 pies) y enrollándolos en carretes de 4 metros (13 pies) de diámetro. El equipo de fondo de pozo incluyó hasta tres portamechas de 4 ¾" de diámetro externo, un motor Dyna-Drill de 5" y un trépano tricono de 6 ¼".
En capítulos anteriores se han tratado los desarrollos de los equipos y los lineamientos básicos de seguridad que deben contemplarse durante los servicios con tubería flexible (CT, por sus siglas en inglés). Aunque las modificaciones realizadas en los equipos han mejorado la confiabilidad de su desempeño y servicio, los últimos avances en tecnología son el resultado de mejoras en su fabricación y manejo.
La tecnología moderna de tubería flexible puede remontarse a la labor emprendida por los equipos de ingeniería de las Fuerzas Aliadas durante la Segunda Guerra Mundial. El proyecto PLUTO (cuyas siglas en inglés significan Ductos por Debajo del Océano) era un plan secreto de invasión de las Fuerzas Aliadas que consistía en el montaje de ductos a través del Canal de la Mancha, desde Inglaterra hasta Francia. Al concluir el Proyecto PLUTO, las Fuerzas Aliadas instalaron 17 ductos para suministrar combustible a las fuerzas Aliadas de invasión. La mayoría de ductos se construyó con tubos de plomo de 3" de diámetro interno (ID, por sus siglas en inglés) y un espesor de pared (WT, por sus siglas en inglés) de 0,175" reforzado con una cobertura exterior de cable trenzado para mayor contención.
Los 11 ductos compuestos por tubos de plomo fueron enrollados alcanzando una extensión total de alrededor de 48 kilómetros (30 millas). Los seis restantes se fabricaron soldando tubos de acero de 3" de diámetro interno, 0,212" de espesor de pared y 12,2 metros (40 pies) de largo para formar tuberías de 1.219 metros (4.000 pies). Estos tramos de 1.219 metros se soldaron entre sí por los extremos y se enrollaron en carretes de extensiones continuas de entre 48 y 113 kilómetros (30 y 70 millas) para su transporte. Todos los ductos PLUTO se enrollaron en tambores flotantes de aproximadamente 12 metros (40 pies) de diámetro con alrededor de 18 metros (60 pies) entre los rebordes. El éxito del enrollado y de la instalación de los ductos a mediados de la década de 1940 preparó el camino para la tecnología actual de tubería flexible.
Desarrollo de la Tubería Flexible
La llegada de los servicios petroleros con tubería flexible a comienzos de la década de 1960 requirió el desarrollo de tubos de menor diámetro externo que pudieran resistir las tensiones y la deformación al enrollarlos en un carrete de diámetro reducido. Los pioneros en el desarrollo y fabricación de tubería flexible intentaron aplicar técnicas de fabricación similares a las empleadas en el Proyecto PLUTO. En 1962, se fabricó el primer carrete de gran escala para tubería flexible utilizando un acero con niobio muy dúctil y de baja aleación. La empresa Great Lakes Steel Co. de Michigan, Detroit, laminaba la placa de acero a un espesor de 0,125" y la compañía Standard Tube Co., también de Detroit, la fresaba en tuberías de 1,315" de diámetro externo.
Los tubos fresados eran de solamente 15 metros (50 pies) y debían soldarse entre sí mediante un proceso combinado de Gas Inerte y Electrodo de Tungsteno (TIG, por sus siglas en inglés) y Gas Inerte y Aporte de Metal (MIG, por sus siglas en inglés). Posteriormente, el tubo se enrollaba en un carrete de 2,7 metros (9 pies) de diámetro. Los resultados de esta primera generación de tubería flexible no demostraron de manera acabada todo el potencial de esta tecnología. No obstante, dejó entrever cuán beneficiosa sería en los servicios de pozo de petróleo y gas.
La compañía Republic Steel, de Brooklyn, Nueva York fabricó la primera tubería en extensiones continuas utilizando un acero de alta ductilidad. El acero era un material de Alta Resistencia y Baja Aleación (HSLA, por sus siglas en inglés) y, salvo modificaciones menores, sentó las bases para la fabricación de la tubería flexible de hoy en día. El acero que tenía un límite elástico que oscilaba entre los 40.000-psi (40-ksi) y los 50.000-psi (50-ksi) venía en placas de 0,049" de espesor. La tubería se fresaba en tramos que variaban entre los 85 y los 610 metros (250 y 2.000 pies) y las sartas se ensamblaban soldando sus extremos mediante las técnicas TIG y MIG. Luego la tubería continua se enrollaba en carretes de 48" de diámetro.
Aunque en un principio el sistema de tubería flexible de Brown Oil Tool creado en 1964, fue construido para tuberías de ¾" de diámetro externo, en los tres años siguientes el sistema se modificó para correr tuberías de ½" de diámetro externo. En 1967, Bowen Tools produjo la segunda generación del sistema de tubería flexible diseñado en un principio para correr tuberías de ½" y ¾" de diámetro externo. A comienzos de la década de 1970, este sistema también sufrió modificaciones para el manejo de tuberías de 1" de diámetro externo.
Southwestern Pipe Inc. Comenzó la fabricación de tubería de extensión continua para CT en 1969. Aunque la resistencia del acero variaba todavía entre los 50-ksi y 55-ksi, las mejoras alcanzadas en su fabricación y tratamiento aumentaron significativamente el desempeño general del tubo. En esa época, Southwestern Pipe se convirtió en el proveedor líder de CT para la industria de reacondicionamiento concéntrico de pozo.
Durante comienzos de la década de 1970, se amplió la gama de servicios prestados con tubería flexible de 1" de diámetro externo, yendo desde el lavado de arena y la descarga de pozos someros a servicios más exigentes a mayor profundidad. Desafortunadamente, la resistencia del material y las numerosas soldaduras necesarias para la tubería continua de 1" de diámetro externo no pudieron resistir los repetidos ciclos de flexión y las altas cargas de tracción asociados a carreras de CT a mayor profundidad. Durante la década de 1970, la reputación de la tubería flexible en la industria del petróleo y el gas se resintió. La falta de confianza de los usuarios fue cada vez mayor debido a las fallas de las soldaduras, los desperfectos en los equipos y las situaciones de pesca de tubería flexible en los pozos.
Como la industria estadounidense de CT lograba progresar en los servicios de reacondicionamiento concéntrico de pozo, una empresa canadiense llamada FlexTube Service Ltd. promovió el concepto de perforación con tubería flexible. En 1976, comenzaron a perforar pozos de 366 a 518 metros (1.200 a 1.700 pies) de profundidad con diámetros internos de 6 ½" utilizando tubos flexibles de 2 3/8" de diámetro externo, para compañías operadoras en Alberta, Canadá. La columna de perforación de 2 3/8" de diámetro externo se construyó soldando los extremos de tubos X-42 de 12,19 metros (40 pies) y enrollándolos en carretes de 4 metros (13 pies) de diámetro. El equipo de fondo de pozo incluyó hasta tres portamechas de 4 ¾" de diámetro externo, un motor Dyna-Drill de 5" y un trépano tricono de 6 ¼".
Quality Tubing Inc. Surgió en 1976 para fabricar tuberías exclusivamente para un proveedor líder de servicios de CT. Pero para el año 1982, estaban proveyendo a toda la industria de este tipo de servicios. El proceso de fabricación adoptado por Quality Tubing era similar al empleado por Southwestern Pipe. En estos tiempos, solamente Quality Tubing y Southwestern Pipe estaban fabricando tubería flexible para la industria de reacondicionamiento concéntrico de pozo. La tubería se estaba fresando en tramos de 457 metros (1.500 pies) y enviando en bultos para aliviar la tensión. En 1978, las mejoras en la calidad de fabricación implementadas por ambas empresas permitieron el desarrollo de una tubería flexible más extensa de 1 ¼" de diámetro externo.
La década de 1980 pareció ser el punto de inflexión para la tecnología CT. En 1980, Southwestern Pipe introdujo el primer material de alta resistencia y baja aleación de 70-ksi de límite elástico. El rendimiento de la tubería de 70-ksi era claramente superior a la anterior de 55-ksi. A comienzos de la década de 1980, el acero con 70-ksi de límite elástico se consideraba el material óptimo para CT, ya que los ensayos con 80-ksi o superiores indicaban una reducción pronunciada en la vida útil de la tubería.
En 1983, Quality Tubing comenzó a recibir placas flexibles de acero japonés de 914 metros (3.000 pies). Las láminas de acero de mayor longitud redujeron en un 50% el número de soldaduras necesarias para ensamblar una sarta. A finales de la década de 1980, Quality Tubing inició el proceso de "soldadura oblicua" de las placas de acero antes de fresar el tubo. El proceso de soldadura
"oblicua" al final de cada plancha de acero plana implica cortar diagonalmente sus extremos y ajustarlos antes de soldar. Este tipo de soldadura mejoró la resistencia y la vida útil de la tubería flexible al extender la zona afectada por el calor de la misma en forma de espiral alrededor del tubo tras el fresado.
En el transcurso de la década de 1980, las mejoras en la fabricación de tubos contribuyeron a promover la tecnología CT en más áreas de servicio. La tubería flexible estaba siendo utilizada en todos los servicios de bombeo, transmisión de herramientas de fondo de pozo y como reemplazo de columnas de producción. También se emprendió el desarrollo de tuberías de mayor diámetro con la introducción de los tamaños de 1 ½" y 1 ¾" de diámetro externo.
En 1990, se fresó la primera columna de tubería flexible de 2" de diámetro externo para la terminación permanente de un pozo. Al poco tiempo, se fabricaron los tamaños de 2 3/8", 2 7/8" y 3 ½" para aplicaciones de servicios de pozo.
Fabricación
Actualmente, existen tres fabricantes de productos tubulares flexibles que proveen el CT utilizado por los proveedores de servicios de todo el mundo. Las compañías Precision Tube Technology, Quality Tubing y SeaCAT, Inc. fabrican productos tubulares flexibles en Houston, Texas. Precision Tube Technology también tiene una planta en Escocia.
Cada uno de estos fabricantes está explorando nuevos avances en tecnología CT. Asimismo, la industria metalúrgica de alta resistencia y baja aleación está trabajando permanentemente en el desarrollo de productos. La mayor resistencia se logra mediante cambios en la química y el tratamiento del acero, tal como el temple y el revenido. Este artículo se focalizará en el proceso tradicional de fabricación de tubería flexible para acero "bruto de laminado" y con tratamiento térmico.
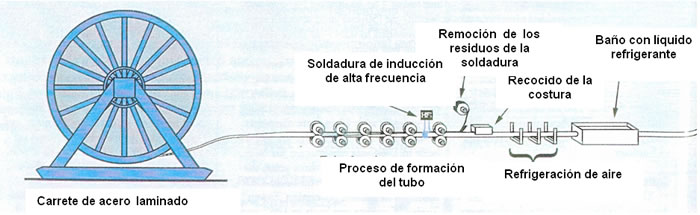
Acero convencional al carbono. La tubería que se emplea en servicios de pozo con CT se fabrica con un acero al carbono A-606 o A-607 Tipo 4. Modificado de alta resistencia y baja aleación con límites elásticos que varían entre los 60 y los 100 ksi. En el cuadro 4.1 se puede observar la lista actual de tuberías flexibles disponibles en la industria, junto con los requerimientos químicos del producto.
El primer paso en la fabricación de CT es la adquisición de placas de acero laminadas de entre 762 y 1.067 metros (2.500 y 3.500 pies) de largo. Una vez elegido el diámetro de tubería a ser fabricado, las chapas laminadas se cortan en Flejes continuos de un ancho específico para formar la circunferencia del tubo. Los flejes de acero se sueldan entre sí por los extremos para formar un rollo continuo de acero de plancha. El área soldada se alisa, se limpia y se inspecciona con rayos-X para comprobar que las soldaduras no tengan defectos. Una vez que se enrolla una extensión suficiente de acero continuo en el carrete, puede darse inicio al proceso de mecanizado (Fig. 4.1).
La placa de acero atraviesa una serie de matrices de rodillos que convierten mecánicamente al fleje plano en un tubo. Como los bordes de la lámina están juntos, se sueldan mediante inducción de alta frecuencia a unas pocas pulgadas del último grupo de rodillos. Se retiran los residuos de la tubería y se recoce la costura de la soldadura a temperaturas de entre 788°C y 927°C ( 1.450°F y 1.700°F ). El tubo se deja enfriar y posteriormente pasa al sector de ensayos no destructivos.
La sarta de tubería continua atraviesa un proceso de fresado de ajuste que lleva al tubo al diámetro externo y tolerancias de redondez requeridos. En esta instancia, el tubo es sometido a un tratamiento térmico mediante bobinas de inducción. El tratamiento térmico a temperaturas que varían entre los 593°C y los 760°C (1.100ºF y 1.400ºF) alivia las tensiones del tubo y aumenta la ductilidad. El tubo se deja enfriar, primero gradualmente por aire y luego por baño líquido. A consecuencia de este proceso, se generan perlitas y ferritas de apariencia granular en la microestructura del acero. Posteriormente, el tubo es enrolla en un carrete de servicio o de transporte de madera y se le realiza una prueba de agua a presión.
Acero aleado templado y revenido (Q&T, por sus siglas en inglés). La tubería flexible templada y revenida generalmente es en un principio un acero de alta resistencia y baja aleación de 80-ksi de límite elástico, con una composición química ligeramente diferente a la del acero convencional de CT. La diferencia más importante tiene que ver con el cromo y el molibdeno, que aportan las caracte- rísticas resultantes de la exposición del acero al tratamiento térmico.
La fabricación es normalmente la misma que la del acero al carbono convencional para tubería flexible sometido al proceso de fresado de ajuste. Después de que el tamaño de la tubería ha sido ajustado mediante fresado, se la calienta a temperatura de solución y se la enfría rápidamente (templado). Como resultado, se forma una microestructura de martensita que le otorga una resistencia extremadamente alta pero baja ductilidad. La tubería se somete posteriormente a un tratamiento térmico extenso y controlado (revenido) que reduce el nivel de resistencia e imparte ductilidad al tubo. El producto final es una sarta de tubería flexible de alta resistencia con propiedades físicas en los 100-ksi y los 110-ksi de límite elástico.
Lamentablemente, junto con los beneficios de mayor resistencia, la tubería de material Q&T tiene una capacidad de reparación limitada. Si la tubería Q&T se suelda para reparación, el nuevo tramo soldado está sujeto a temperaturas de fusión que regresan el material a su límite elástico original de 80-ksi. El tramo afectado debe entonces atravesar un tratamiento Q&T, tal como se describió anteriormente para aumentar el límite elástico en el área soldada. Como esto no es práctico en el campo, la tubería debe clasificarse con su límite elástico inicial después de una falla en el campo.
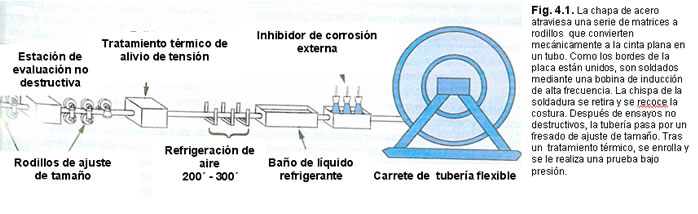
-Fin Parte 1-
Fuente: Petróleo Internacional
5226 lecturas | Ver más notas de la sección Novedad Técnica