Desde el 2002 al 2004, las actividades de perforación con Coiled Tubing en pozos horizontales crecieron aproximadamente de 3.000 m a 70.000 m ( 9843 ft a 229.659 ft ) por año. Mientras CTD se convertía en tecnología confiable, más operadores comenzaban a considerar los nuevos desarrollos de conjunto de fondo de pozo (BHA)para proyectos de perforaciones en desbalance (UBD).
Backer Hughes INTEQ ha diseñado el sistema de CoilTrak controlado por el CTD/ BHA (cuadro 1) para el funcionamiento confiable y de alto rendimiento para los motores de fondo en ambientes rigurosos, altas temperaturas de 150° C (300° F), vibraciones severas, límites excedidos porla velocidad de motores, e intrusión del nitrógeno en BHA y elastómetro de los estatores de dichos motores.
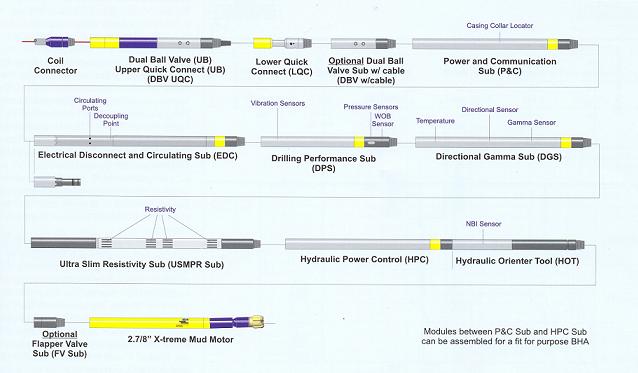 |
|
El diseño de BHA CoilTrak se basa en las en las experiencias de los operadores. Este artículo comparte lo aprendido usando el sistema de CoilTrak en el norte de Sharjah, de Argelia y de Alaska. Estos proyectos se han reconocido y el éxito económico, y las experiencias de estos pozos, se pueden aplicar para optimizar la secuencia de perforación y para el funcionamiento óptimo en otros ambientes desafiantes.
CTD desafía altas vibraciones en flujo polifásico
Las vibraciones de la columna de perforación (Drill string) son principalmente debido a la acción de corte del trepano con la formación y el contacto del BHA en la pared del pozo. Estas vibraciones generan los movimientos axiales, laterales y torsionales, que pueden conducir a los efectos catastróficos sobre el conjunto de perforación. Las vibraciones severas de las columnas pueden afectar el éxito total de una operación, causando (twist -off) rotura por torsión, fallas del trepano, bajo índice de penetración y falla de componentes mecánicos y eléctricos del BHA.
Underbalanced Drilling / Flujo Polifásico
Para perforaciones en Desbalance el flujo monofásico, perforaciones liquidas (Ej., petróleo crudo, diesel y otros a base de aceite) que se utilizan a menudo son altamente reactivos y dañan a los componentes del elastómero y podrían limitar la confiabilidad y durabilidad del BHA. En la fase de planeamiento del proyecto, es crítico unir varios componentes del BHA al líquido que perfora. Los líquidos polifásicos, o sea, la mezcla del nitrógeno y del líquido, pueden estropear el elastómero debido a la hinchazón, así como las altas vibraciones, cavitacion, que podrían causar errores de los componentes electrónicos.
Detección de Vibraciones
Los avances recientes en tecnologías de CTD han proporcionado los medios para medir vibraciones del pozo. La Vibración Stick-Slip (VSS) censores en el BHA de CoilTrak CTD proporciona los datos en tiempo real de los esfuerzos dinámicos de la columna perforadora y permite ajustar parámetros mientras que perfora para evitar o reducir los daños que se puedan originar.
El modulo VSS es parte del (DPS) Drilling Performance Sub que contiene integrados la presión del pozo y los censores de peso sobre el trepano (WOB = Weigth on bit). Los datos se muestrean, se filtran y procesan a partir de tres acelerómetros en X, Y y Z. Se calculan todos los niveles del choque usando (g-RMS) para proporcionar un índice de la vibración lateral y axial de la columna perforadora.
Puesto que el BHA es un sistema de perforación por cable, los datos del pozo se trasmiten a la superficie cada 5-8 segundos, permitiendo que la perforadora haga las correcciones inmediatas basadas en información visible en la pantalla, en tiempo real. Tres colores en barras, similares a un semáforo, alertan a la perforadora de vibraciones laterales, axiales y/o torsionales potencialmente catastróficas. La clave del éxito del sistema es que es fácil de entender y utilizar, con una barra verde que indica el buen funcionamiento y las luces amarillas y rojas que indican la presencia de vibraciones perjudiciales. La meta fundamental en la gerencia de las vibraciones es reducirlas al mínimo ajustando el RPM, WOB y Caudal. Las ventajas del manejo de las vibraciones incluyen calidad de la perforación, reducción del tiempo muerto y ahorros en gastos de explotación.
Ajuste de procedimientos y de parámetros de perforación
Al perforar con 3 pulgadas, el CT BHA en el programa de desarrollo de UB, en el campo de Sharjah, los parámetros utilizados para perforar fueron modificados en base a las experiencias utilizando el módulo del VSS. El VSS midió los cambios en respuesta a las vibraciones del pozo que resultaron de cambios específicos en la perforación. Las vibraciones críticas aparecen principalmente cuando el BHA está en el fondo. De acuerdo con esta experiencia, los procedimientos fueron ajustados para bajar la secuencia de movimientos y para limitar la frecuencia de limpieza del pozo a un mínimo aceptable. Con el VSS \'Traffic Light\' (\' las advertencias semáforo \') exhibidas en la cabina de control de CT, la perforadora y el operador de CT redujeron al mínimo las vibraciones criticas de daño ajustando eficientemente los parámetros y procedimientos.
Ajuste De la Configuración del BHA
Sobre un extenso programa de dieciocho meses, muchos ensayos fueron conducidos para reducir las vibraciones del BHA. Los ensayos incluyeron la fabricación de piezas para un diseño más flexible, examinando el diseño del trepano y el aumento de la estabilización en la parte inferior del BHA. Con estos procedimientos, las vibraciones críticas de daño fueron aisladas antes de que causaran roturas a los sensibles componentes electrónicos. La experiencia hasta la fecha ha proporcionado datos útiles en tres categorías principales:
1-Diseño de Trepano (Bit desing)
2- Longitud y flexibilidad del BHA entre la electrónica - motor/bit
3-Peso de BHA
Lo mas crítico del trepano es cuando causa la vibración en el fondo, el motor se permite girar rápidamente sin carga. En una condición de "cero carga", una gama de 500-960 RPM es normal. Cualquier desequilibrio leve en el trepano causará vibraciones laterales que dañaran y podrían conducir a fallas. Los diseños de trepano fueron probados de muchos proveedores y el que proporcionó menos vibraciones en el pozo fue el de 3 pulgadas PDC Bit.
La distancia entre el motor y la electrónica del sistema CTD fue optimizada para reducir al mínimo la transferencia de vibraciones críticas del BHA. La longitud del BHA fue aumentada introduciendo barras del peso. Un conector o sustituto flexible fue agregado entre las barras de peso para que sirvan como vibración simple y desacoplen el mecanismo.
Finalmente, el peso del BHA fue aumentado usando sistema de cobertura externo de la herramienta con un peso hasta cuatro veces más alto comparado al diseño original. El peso adicional actuaba como ancla al BHA en situaciones de perforación laterales y permitió que las vibraciones fueran transferidas inofensivamente a la pared del pozo. Con los tres diseños, las ediciones que se pusieron en práctica y los resultados del VSS demostraron una importante reducción en vibraciones críticas.
El cuadro 2 muestra un ejemplo de las vibraciones consideradas en una pasada del limpiador fuera del pozo antes de que las coberturas fueran introducidas. - con alta tendencia de vibraciones rojas-.
El cuadro 3 proporciona un ejemplo de las vibraciones después de la introducción de la cobertura, se observa que mientras todavía hay algunas vibraciones rojas, los incidentes son menos frecuentes y de menor duración.
Mejorar electrónica del BHA
Resultado de Control de Vibración
Las experiencias con los resultados de control de vibración resultaron con mejoras y con un positivo impacto en el funcionamiento de la unidad de CTD. El éxito en los campos de Sharjah fueron los de 10.000 ft/25 por día (3050 m/25 día) (400 ft/ día o 122 m/día). La cuadro 4 muestra la mejora continua en un cierto plazo.
Al principio, el funcionamiento del proyecto era muy pobre y a través de bastantes ensayos con prueba y error se pudo aprender y manejar el equipo.
Compatibilidad del elastómero en Flujo Polifásico
Diversos tipos de gases se pueden utilizar para la perforación de flujo polifásico. El gas natural, así como el nitrógeno, contiene alto oxígeno dando por resultado corrosión en el coiled tubing y otros componentes. Para evitar los problemas de corrosión generalmente lo que favorece a las perforaciones de gas es el nitrógeno. En anteriores experiencias mientras que perforar con nitrógeno revelaba que el elastómero en BHA absorbe nitrógeno cuando presuriza y, cuando despresurizar, el elastómero experimenta dificultad para lanzar gas. Este gas de retención puede conducir a la destrucción del elastómero y causar faltas en las conexione eléctricas o en el pozo. El nitrógeno daña al elastómero mientras dispara, y también tiene un efecto ablandamiento en el elastómero durante cierto periodo. Este efecto se pudo observar en el laboratorio y mientras se perforaba.
Elastómeros en el sistema CTD
CTD BHA contiene varios componentes elastómeros incluyendo empalmes o conectores eléctricos, cables y línea eléctrica en coiled tubing. Para el campo de Sharjah hubo que proyectar donde perforar con CTD porque el nitrógeno era liquido y tenia pequeñas cantidades de agua. La prueba de laboratorio de descompresión de nitrógeno se realizo en los pozos bajo temperaturas adecuadas.
Con esta prueba se pudo identificar específicamente cual era el componente que lo afectaba(cuadro 5) . De acuerdo con este resultado, un nuevo componente con mejoras en el material se ha desarrollado para hacer frente a las condiciones de perforación.
Fin Parte 1
Además de detectar vibraciones y de aplicar las mejores prácticas, las mejoras fueron llevadas a cabo al diseño electrónico del tablero. Algunas de las iniciativas dominantes incluyeron cambiar los componentes del tablero por piezas más livianas en peso y utilizar otros materiales. Estas mejoras fueron hechas para alcanzar un espacio óptimo entre los componentes electrónicos y la cobertura. Las Pruebas del calibrador, como parte de la investigación y del proceso de fabricación, ayudaron para asegurarse de que la distancia apropiada entre los componentes, la cubierta y el espaciamiento fueron optimizados para reducir el efecto de vibraciones negativas en tableros y marcos.
Fuente: Baker Hughes
5045 lecturas | Ver más notas de la sección Novedad Técnica